- 公司:DURA Automotive Systems
- 国家:印度
- 产业:汽车
- 解决方案:Moldex3D Advanced Package; Flow, Pack, Cool, Warp, Designer BLM, Viscoelasticity
DURA Automotive Systems 为国际化汽车供货商,专精于设计和制造解决方案,推动汽车产业的革新。DURA具备了超过100年的研发经验,在创新、整合、机电系统和轻量化解决方案等各方面,都被视为具领先地位的优质厂商。(来源: https://www.duraauto.com/)
大纲
本案例产品为汽车窗户的包边件,包含三个嵌件:透明玻璃、玻璃滑道(GRC)及小的铝制嵌件。其中玻璃滑道的变形造成产品无法满足间隙面差的要求,进而导致组装困难。DURA Automotive工程师利用Moldex3D找出变形的主因,由于PVC厚壁和GRC接触,导致产品功能问题。DURA Automotive工程师于是利用ABS嵌件来减少产品厚度与变形,同时保有强度。透过Moldex3D模拟工具辅助,DURA Automotive 能有效优化产品设计,进而改善翘曲,顺利进行产品组装。
挑战
- 翘曲导致组装困难
- 凹痕
- 缩短冷却时间
解决方案
DURA利用Moldex3D验证GRC的改良设计,以解决翘曲、冷却和凹痕问题
效益
- 改善流动平衡
- 降低X方向变形量80%,满足间隙面差需求,顺利进行组装
- 消除凹痕
- 缩短冷却时间66%
- 缩短开发周期
案例研究
DURA的车窗包边件面临无法满足间隙面差要求的问题。该产品由透明玻璃、玻璃滑道(GRC)及小的铝嵌件三种嵌件所组成,并以PVC材料包覆(图一、图二)。虽然GRC旁的PVC厚度是造成变形的原因,但为了达到组装需求,DURA仍不能牺牲此PVC厚度。
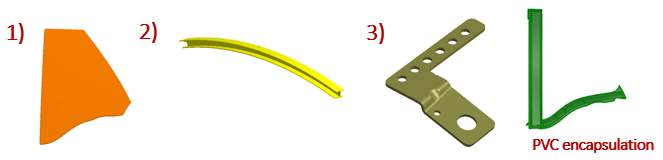
图一 车窗包边件嵌件:(1)透明玻璃、(2)玻璃滑道(GRC)、(3)铝嵌件
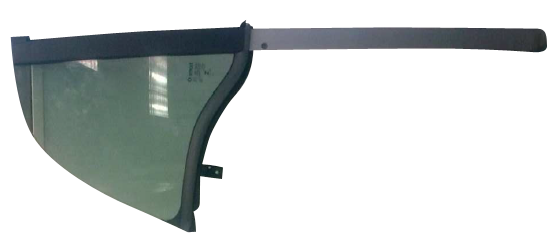
图二 实际组装图
然而在成型之后,由于产品不均匀收缩和PVC的冷却问题,导致GRC在X方向产生5 mm的变形(图三),而使得实际组装时,产品无法满足间隙面差的要求,也因此无法顺利组装。DURA于是利用Moldex3D来分析现行问题之间的关联,并找出GRC偏差的原因(图四)。
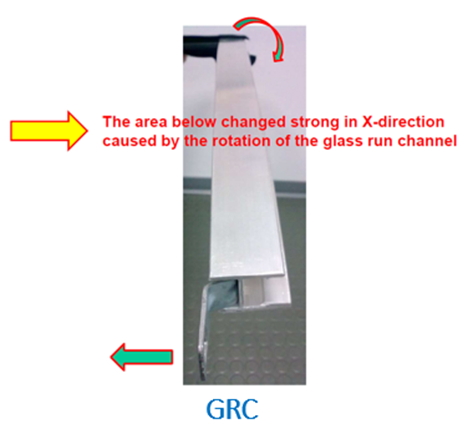
图三 GRC的变形问题
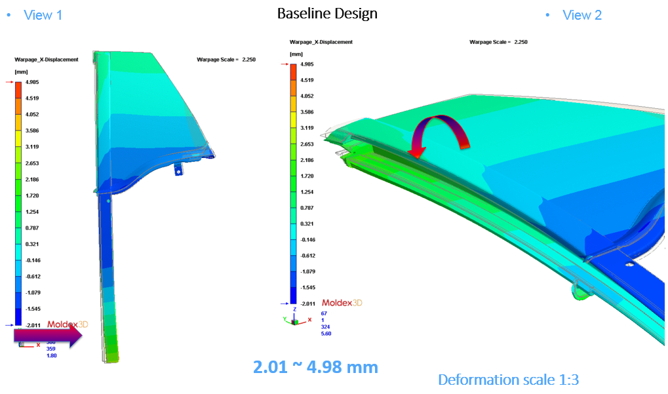
图四 Moldex3D翘曲分析结果,捕捉到GRC在X方向有5mm的变形
Moldex3D分析结果显示GRC变形问题,DURA藉此找出成因,包括GRC旁的PVC厚度不均(图五)、冷却结束时产生的热点(图六) 、不均匀的产品收缩,以及不充足的冷却时间等。而造成冷却问题的原因,是受限于产品成本的关系,因此DURA必须缩减冷却时间。除此之外,在冷却时间结束时,还发生凹痕问题(图七)。
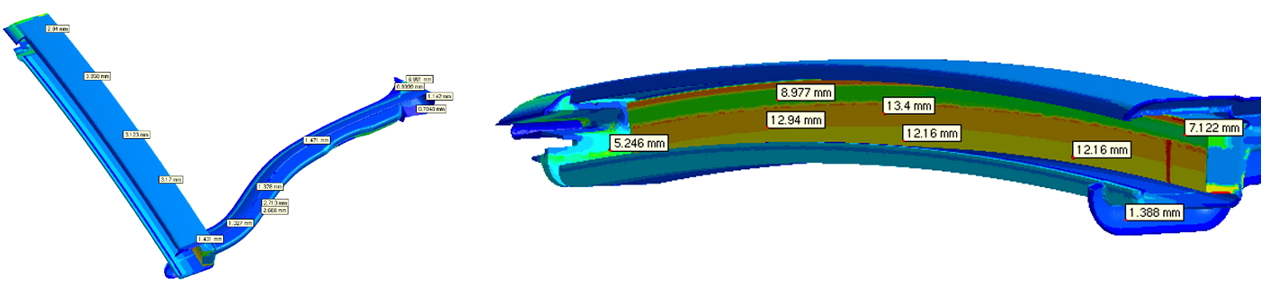
图五 本产品的厚度不一,最厚区域为13.4 mm,最薄区域为0.5 mm
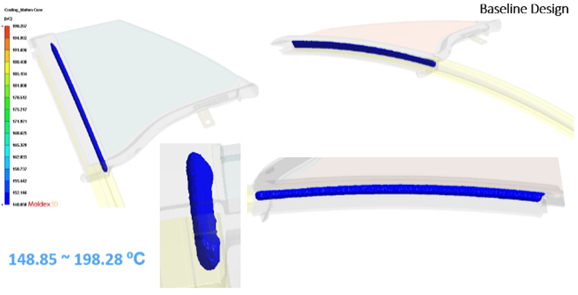
图六 塑件熔融区域的等位面图,显示出产品在冷却结束时,核心仍有熔融的现象
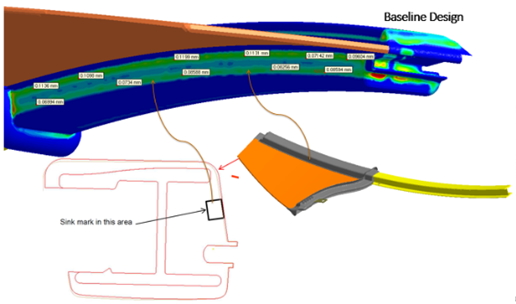
图七 冷却结束时发最深的凹痕有0.1 mm
为了改善变形问题,DURA多次的产品设计和制程参数修改,仍无法达到间隙面差要求。因此他们决定在设计变更时,加入一个ABS嵌件,如此就不必牺牲产品厚度(图八、图九)。DURA并同时透过Moldex3D进行设计变更的模拟验证。
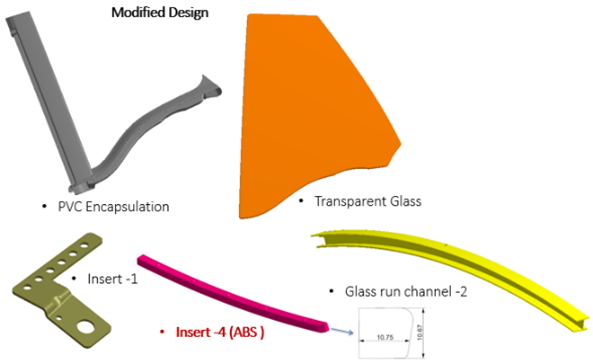
图八 修改后的产品设计
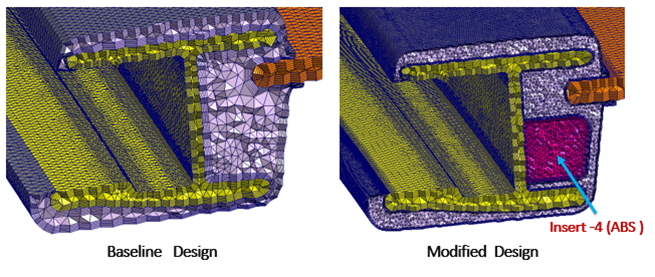
图九 原始设计及设计变更的网格图,设计变更中多了一个ABS嵌件
DURA最后成功找到了优化的设计,根据Moldex3D的分析结果来调整,有效改良翘曲问题(图十、图十一)、并克服组装难题。同时所需的冷却时间也由112秒缩短至38秒(图十二、图十三),凹痕问题也获得解决(图十四)。
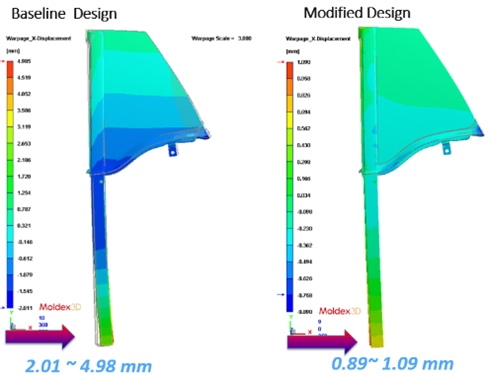
图十 修改设计后,X轴方向翘曲由5 mm缩减为1 mm
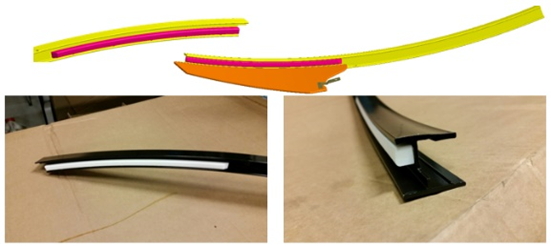
图十一 实际组装图也显现加入ABS嵌件后,X轴方向翘曲缩减为1 mm
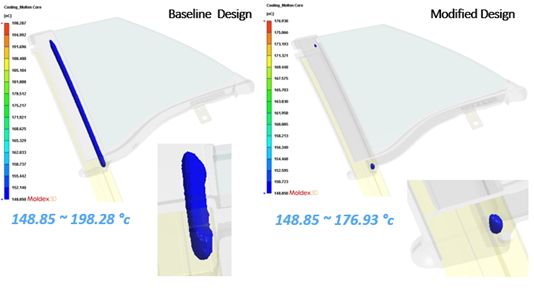
图十二 塑件熔融区域等位图显示,加入ABS嵌件后,核心熔融的问题已改善很多

图十三 加入ABS嵌件后,所需的冷却时间缩短了,到达顶出温度时,只需35至40秒便足够
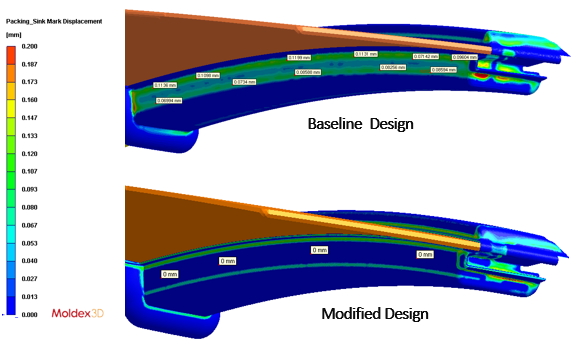
图十四 凹痕由0.1 mm改善为0 mm
结果
DURA使用Moldex3D验证产品设计变更方案,发现将ABS嵌件放在肉厚处不但不会减弱产品强度,同时能减少GRC厚度近85%。Moldex3D协助DURA Automotive成功找出影响变形的原因,并且验证优化后的方案可以有效降低翘曲、凹痕及优化成型周期(表一)。